Plastic extrusion for pipes, sections, and custom shapes
Plastic extrusion for pipes, sections, and custom shapes
Blog Article
Exploring the Numerous Strategies and Technologies Behind Plastic Extrusion
The realm of plastic extrusion is a blend of innovation, modern technology, and precision, crucial to countless markets worldwide. Advanced equipment, digital controls, and a selection of products merge in this intricate procedure, generating top notch, resilient items.
Recognizing the Essentials of Plastic Extrusion
The process of plastic extrusion, commonly hailed as a cornerstone in the realm of production, forms the bedrock of this conversation. Essentially, plastic extrusion is a high-volume manufacturing procedure in which raw plastic product is melted and developed right into a continuous profile. It's a method widely utilized for producing items with a continuous cross-sectional account, such as pipelines, home window frames, and weather removing. The process starts with feeding plastic products, typically in the kind of pellets, right into a warmed barrel. There, it is mixed and heated up until it comes to be molten. The liquified plastic is after that forced through a die, shaping it into the wanted form as it solidifies and cools.
The Duty of Various Products in Plastic Extrusion
While plastic extrusion is a commonly used strategy in production, the products made use of in this procedure substantially affect its last output. Different sorts of plastics, such as polyethylene, abs, and pvc, each provide special residential or commercial properties throughout product. Polyethylene, understood for its toughness and adaptability, is commonly utilized in product packaging, while PVC, renowned for its toughness and resistance to environmental factors, is utilized in building and construction. ABS, on the other hand, combines the ideal characteristics of both, causing high-impact resistance and toughness. The option of material not just impacts the item's physical residential or commercial properties but likewise affects the extrusion rate and temperature level. Makers must carefully think about the residential or commercial properties of the product to enhance the extrusion process.
Techniques Used in the Plastic Extrusion Process
The plastic extrusion procedure entails numerous techniques that are essential to its operation and effectiveness (plastic extrusion). The discussion will certainly start with a streamlined description of the essentials of plastic extrusion. This will certainly be adhered to by a malfunction of the process thoroughly and an expedition of techniques to improve the effectiveness of the extrusion technique

Comprehending Plastic Extrusion Fundamentals
In the world of production, plastic extrusion stands as an essential process, important in the production of a multitude of day-to-day things. At its core, plastic extrusion entails changing raw plastic material into a constant profiled shape. This is attained by thawing the plastic, usually in the kind of pellets or granules, and requiring it through a designed die. The resulting item is a long plastic item, such as a panel, pipeline, or wire covering, that retains the form of the die. This cost-efficient technique is highly functional, able to develop complicated forms and fit a wide array of plastic products. Fundamental understanding of these essentials enables further expedition of the more detailed aspects of plastic extrusion.
Comprehensive Extrusion Refine Break Down

Improving Extrusion Strategy Performance
Effectiveness gains in the plastic extrusion procedure can considerably impact both the high quality of the last item and the overall efficiency of the procedure. Continual optimization of the extrusion technique is essential to maintaining a competitive edge. Routine upkeep of additional hints extrusion tools can additionally reduce downtimes, therefore boosting performance.
Just How Technology Is Changing the Face of Plastic Extrusion
The introduction of brand-new technology has considerably transformed the landscape of plastic extrusion. It has caused the advancement of advanced extrusion machinery, which has improved the efficiency and quality of the plastic extrusion process. Developments in the extrusion process have additionally been driven by technical improvements, providing improved capacities and convenience.
Advanced Extrusion Equipment
Reinventing the realm of plastic extrusion, advanced equipment imbued with innovative innovation is introducing a new age of effectiveness and precision. These equipments, outfitted with cutting-edge attributes like self-regulating temperature control systems, make certain ideal conditions for plastic handling, consequently minimizing waste and enhancing item quality. High-speed extruders, for example, magnify output prices, while twin-screw extruders provide premium blending capabilities, essential for producing intricate plastic blends. Furthermore, computerized control systems use unmatched accuracy in procedures, minimizing human mistake. These machines are created for longevity, reducing downtime and upkeep expenses. While these advancements are currently remarkable, the constant advancement of technology assures also greater leaps onward in the field of plastic extrusion machinery.
Developments in Extrusion Processes
Using the power of modern-day innovation, plastic extrusion processes are undergoing a transformative metamorphosis. Developments such as electronic mathematical control (CNC) systems currently enable even more accuracy and uniformity in the production of her latest blog extruded plastic. Automation even more improves effectiveness, minimizing human mistake and labor expenses. The combination of man-made intelligence (AI) and artificial intelligence (ML) algorithms is transforming quality control, predicting deviations, and boosting the total efficiency of extrusion procedures. With the development of 3D printing, the plastic extrusion landscape is likewise broadening into new worlds of possibility. These technological developments are not only improving the quality of extruded plastic items yet additionally driving the industry in the direction of a more sustainable, effective, and innovative future.
Real-World Applications of Plastic Extrusion
Plastic extrusion, a reliable and versatile process, locates use in countless real-world applications. The automobile market likewise uses this modern technology to create components like plastic and trim sheeting. The toughness and versatility of plastic extrusion, paired with its cost-effectiveness, make it an important procedure throughout numerous sectors, underscoring its prevalent practical applications.
The Future of Plastic Extrusion: Predictions and Trends
As we seek to the horizon, it ends up being clear that plastic extrusion is poised for considerable developments and improvement. New modern technologies assure to change the market, from intelligent machinery that makes best use of performance to lasting products that lower ecological effect. Automation and robotics are projected to play a bigger duty, enhancing production and guaranteeing constant quality. Environmentally friendly alternatives to traditional plastic, such as bioplastics, are additionally expected to acquire traction. These products not only help to preserve sources but also lessen waste, lining up with global sustainability goals. On the other hand, developments in 3D printing are predicted to open new possibilities for personalization. These fads suggest a dynamic, progressing future for plastic extrusion, driven by technological technology and a dedication to sustainability.
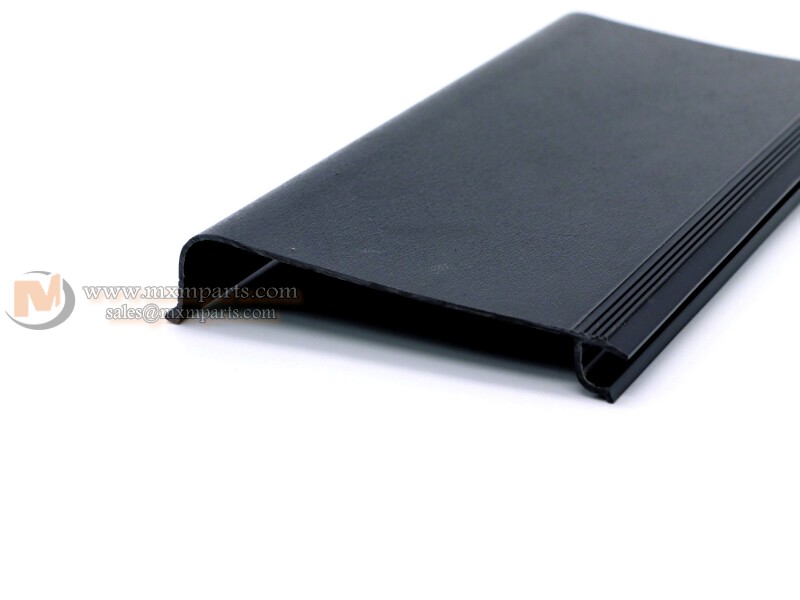
Final thought
Finally, plastic extrusion is a complicated procedure that makes use of advanced innovation and differed products to develop varied products. Technical advancements, such as electronic controls, boost the manufacturing procedure and guarantee regular results. The industry's focus on sustainability and intelligent machinery suggests an appealing future. As plastic production proceeds to progress, it continues to be a vital part of numerous markets worldwide.
In essence, plastic extrusion is a high-volume manufacturing process in which raw plastic product is thawed and created into a continuous profile.While plastic extrusion is a commonly used strategy in production, the materials used in this process significantly influence its final result. At its core, plastic extrusion entails changing raw plastic material right into a continual profiled shape. It has led to the advancement of sophisticated extrusion machinery, which has actually enhanced the efficiency and quality of the plastic extrusion procedure.In final thought, plastic extrusion is an intricate procedure that uses advanced modern technology and differed materials to develop diverse items.
Report this page